Maker Mind MelD Summit
Simon Gao – The Manufacturing Process of a Printed Circuit Board
What happens to your Gerber files once you submit them to an online PCB manufacturer? In this presentation, Simon Gao will go into the details of the manufacturing process at PCBWay, a full-service Printed Circuit Board manufacturer.
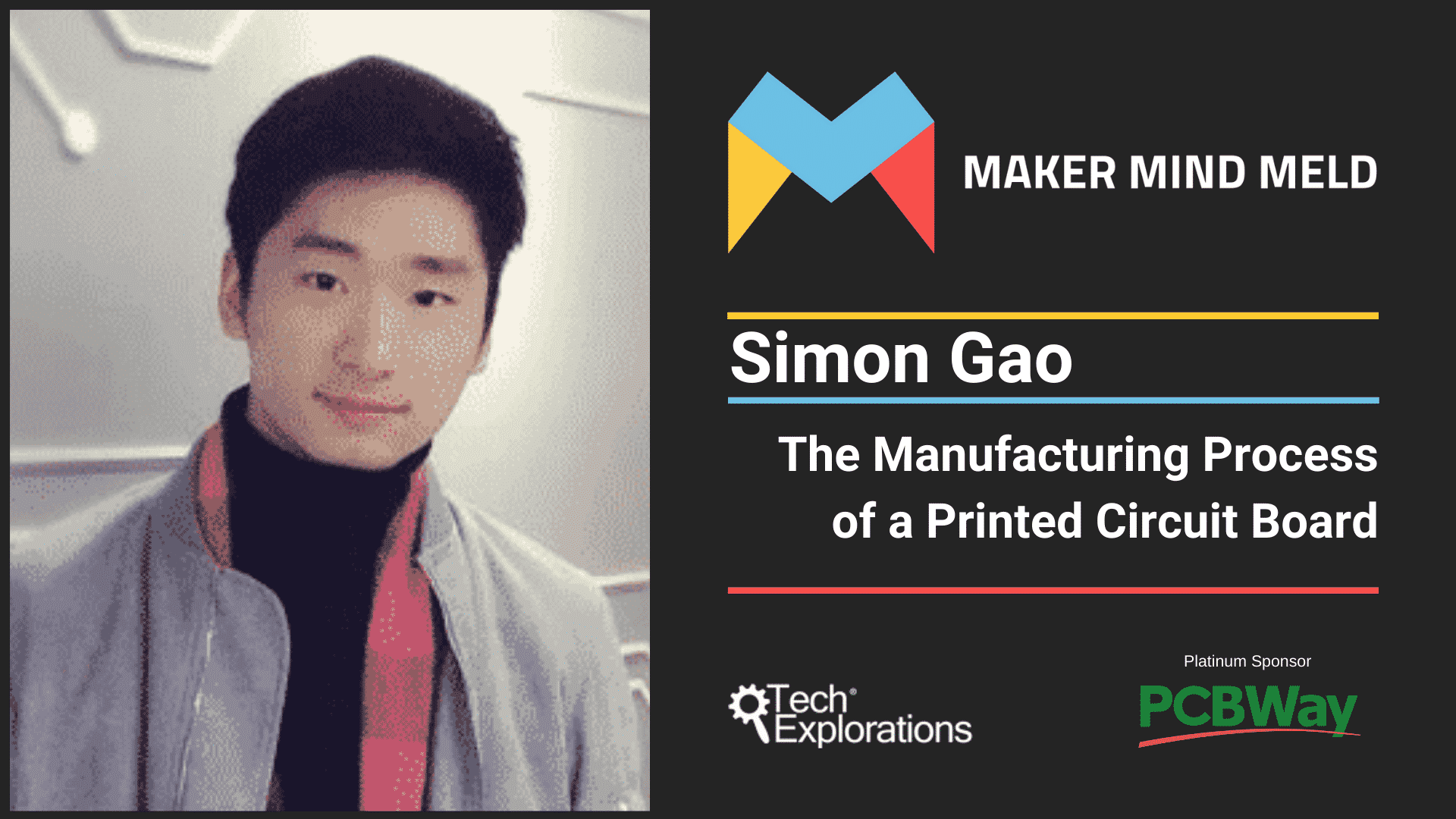
PCBs play a significant role in connecting all functions in a complete electronic product. When electronic products fail, the primary suspect is the PCB. Due to the processing technology of PCBs being relatively complicated, the quality control during PCB production is of vital importance and notably precise.
A lot of makers and electronic enthusiasts are curious about the manufacturing process of a PCB. In his presentation, Simon takes us through each of the 14 distinct steps. From cutting the substrate material into the appropriate shape and size for your board to the final quality control, there’s a lot that has to happen to produce a high-quality PCB. There’s the pre-treatment, lamination, exposure, development, etching, stripping, and that’s only the beginning.
Knowing how PCBs are made in the factory will give you a more in-depth insight into the process which you can use to design PCBs that are easier, cheaper, and better to manufacture.
Watch full video below
Transcript
Peter Dalmaris: Hi everyone, and welcome to this special Maker Session. In this session, Simon Gao from PCBWay, a fully featured printed circuit board manufacturer, will take us deep into the manufacturing of printed circuit boards.
Peter Dalmaris: I'm Peter Dalmaris, an online educator and maker, author of Maker Education Revolution, and founder at Tech Explorations. My mission is to help people learn electronics, programming, printed circuit board design, and lots more. Most importantly, though, I want to help as many people as possible to enjoy the technology education adventures.
Peter Dalmaris: As I said, in this session, my guest speaker is Simon Gao. Simon is a Customer Experience Manager with PCBWay with a five-year experience in the PCB field. From this position, Simon became intimately familiar with what happens in the factory floor as soon as you upload your Gerber files.
Peter Dalmaris: The manufacturing process includes 14 distinct steps, from cutting the substrate material into the appropriate shape and size for your board to the final quality control. There's a lot that has to happen to produce a high-quality PCB. There's the pre-treatment, lamination, exposure, development, etching, stripping. And that's just the start.
Peter Dalmaris: Knowing how PCBs are actually made in the factory will give you a deeper insight into the process, which you can use to design PCBs that are easier, cheaper, and better to manufacture.
Peter Dalmaris: So, Simon, thank you for joining me today and for taking the time to explain how PCBs are made. How are you doing?
Simon Gao: Hello, everyone. I'm Simon from PCBWay. I'm really excited to be here during this summit. And, yes, really excited and a little bit nervous. Thank you for inviting me here.
Peter Dalmaris: It's my pleasure. This is going to be fun. And I do have a question to kickstart your presentation within that. It may go a little bit back in time when I was much younger and I was an engineering student. I remember that when I was designing my first PCBs, that was back in their mid '90s, I had to print the circuit board in an inkjet printer and then take the paper to a small fabricator in the city where I was studying.
Peter Dalmaris: They didn't have email, of course, I couldn't upload it or email it. I had to take the paper to the manufacturer. So then, it would take them about a week to do whatever they had to do. I didn't really know how they did what they did. They would produce a single board. It was very expensive. It looked ugly. But it did work. Electrically, it was okay. But, you know, it wasn't a good experience, and I always try to avoid making PCBs. I rarely designed PCBs to make them through the manufacturing process.
Peter Dalmaris: But, now, these days, it's so easy. It's totally different. I can upload my designs. They're made quickly, cheaply, high quality. I can't see the difference between my PCBs and what I see in a finished product that I buy at a shop.
Peter Dalmaris: I wanted to ask you about your opinion, what are the one or two most important developments in the PCB manufacturing business that are responsible for this amazing shift, the difference between how things were done in the '90s and even later, and how things are done today?
Simon Gao: Yes. As you said, the PCB manufacturing industry has undergone great changes in recent decades. In my opinion, I think there are two main reasons for this. The first one is continuous breakthrough and innovation of technology products. Now, we can see many equipments, machines - in my later presentation - with more convenient operation and high efficiency to produce high quality products in less time. That's the first important reason because we can produce it in less time, faster, and with high efficiency.
Simon Gao: And the other reason, I think, is, of course, the rapid development of the internet. Yes, the internet directly connects makers and factories. As we can find, the traditional manufacturers nowadays can hardly meet the increasing needs of prototyping orders from makers. Because, for them, it is not a very effective way to produce several boards for many different users.
Simon Gao: But, nowadays, you don't have to go to the factories in person, just as you said, and bring your paper. That is very complicated. On the contrary, you just need a few clicks with a mouse in front of the computer, check out PCBWay website, and fill the parameters, upload the Gerber files, then we will prepare the production in minutes.
Simon Gao: Actually, PCBWay combined the two factors together to build the Online Instant Quote System, which made everything much easier. I think, nowadays, more and more manufacturers start to notice these two factors to improve their service.
Peter Dalmaris: So, it doesn't matter whether you order one PCB or a thousand, the cost will come down, of course, if you order more. But the process is the same, right?
Simon Gao: Not really. Actually, in the past decades, because our machine is continuously improving, so the PCB manufacturing process can be a little bit different than before.
Peter Dalmaris: Right. So, if you order a large volume for a business and you want to build a product for the mass market, then the process that you follow to develop those PCBs to manufacture them will be different compared to if you're just ordering a single unit by a hobbyist?
Simon Gao: It's doing nothing with quantity, actually. No matter the prototyping orders or large amount orders, the process is almost the same.
Peter Dalmaris: Yeah. That's what my impression was as well, so thank you for confirming that. Okay. Well, I'm eager to learn how you do what you do in your factory with this amazing big machines that you have. So, the virtual floor is yours. Show us how it's done.
Simon Gao: Okay. Today, I'm going to introduce you guys some information about PCB fabrication. As we all know, PCB plays a really significant role in connecting all the functions in an entire electronics products. When the function of electronics fails, the first one to be suspected is a PCB. And because a precision technology of PCB is relatively complicated and then the production control of the PCB is particularly strict and important.
Simon Gao: Now, I assume you already know some basic knowledge of PCB, such as what is PCB. And so, let's go to the main points about how to produce it. Before I ran for production, we surely need your Gerber files. If you ever place an order on PCBWay, then you will notice that it will take minutes for us to check your files after you upload it.
Peter Dalmaris: Our DFM engineer, which refers to Design For Manufacturing engineer, will give a brief check to see if any problems with your Gerber files and if it is beyond our capabilities. After checking several Gerber files, the production engineer will combine the boards with different sizes on a large production panel, which is much more efficient to handle through the factory. Thus, production cost also decreases.
Peter Dalmaris: Simon, can I ask you something here? The engineer at this stage is looking at what specifically? Whether the drills, for example, are too small or too large, or maybe the tracers geometrically are too small, too close to each other. What are the two or three things that the engineers are looking at, at this point?
Simon Gao: At this stage, our engineer will, yes, check the parameters of the boards of the designs. When a client uploads Gerber files to our system, they will fill out the parameters first. Sometimes they don't notice that some of their parameters are not right than what they filled out. So, we need to correct the parameters they filled and send them. If anything wrong, we will notice them that, for example, the hole size is smaller than what you filled out and the price will increase. Or some small mistakes with your Gerber files if you need to change it or correct it. If your Gerber file is a complete one.
Peter Dalmaris: Yeah. So, they do checks like that. But what about checks like if a design client has forgotten to connect to pins together, like electrical kind of checks, do you do any of those or those are not your responsibility at that point?
Simon Gao: Normally no. Because sometimes we can't know what the client think about, that's their purpose to design that file. So, normally, we don't interface the designs.
Peter Dalmaris: So, you check for things that affect manufacturing, right? Like, as I said, holes that are too large or too small, so you don't have a drill for that. Or issues that affect the price, so the customer may think that the board, based on the specifications that they provided, may cost $10. But when you look at the Gerber's that they provided, you see that that board would cost $15. It can still be manufactured. The price is going to be different. So then, you have to let them know about that. The two tests you do.
Simon Gao: Yes.
Peter Dalmaris: Yeah. All right. Thank you.
Simon Gao: No problem. Okay. After making sure everything is right, then we can proceed to go through the production line. The first step is to cut the boards. We need to get the raw material first and cut it into required size, which will fit the machine best in the production lines and also very convenient for engineers to panelise the boards according to the required size. The final purpose is, of course, to improve the production efficiency.
Simon Gao: I prepared a short video. You can check our material warehouse.
Peter Dalmaris: So, these are piles of copper boards, right? Very large sheets, copper top and bottom, on shelves?
Simon Gao: Yes. Copper board. We just cut it. Yes. So, you can find in our warehouse, even though they are a lot of copper boards, they have different specifications, like the preferred thickness or other parameters.
Simon Gao: And after getting the substrate material with the right size, the board need to go through the pre-treatment line, which aims to remove contaminants on the copper surface and increase the roughness.
Peter Dalmaris: Like, dust [inaudible].
Simon Gao: Yes. Increase the roughness to facilitate subsequent lamination process. As we can see from the picture, after the pre-treatment, the copper surface became rougher.
Peter Dalmaris: So, why do you want the surface to be rough instead of nice and shiny?
Simon Gao: We make the copper surface to be rougher because it were easier for us to film lamination, the third step.
Peter Dalmaris: Because the film sticks easier on a rougher surface, otherwise it would slide away.
Simon Gao: Yeah. That's the point. And the third step, we'll go to the film lamination. We need to apply the dry film to the treated copper through hot lamination. A dry film, actually, is a key to the formation of circuits, which is very light sensitive. I mean, UV light sensitive and cannot directly receive the ultraviolet radiation. You can see later in our workshop, the light in the entire workshop is dark brown. I will show you a video. The light is dark brown in the entire workshop.
Peter Dalmaris: So, there is no UV in this light to prevent the film from being destroyed, basically, or dissolved by the light, right?
Simon Gao: Yes. And in our factory, we use a memory press machine to complete the film applying process in just a few seconds. As you can see from the video, the dry film is being applied on the surface of the board, but it's not very obvious.
Peter Dalmaris: Yeah. Of course. But the thing that gives the colour and the shyness on that board is the film.
Simon Gao: Yes. And after the dry film is applied, it's time to develop the circuits. Now, we already know that dry film is very light sensitive, so we use it to transfer the image from the original film to the photosensitive substrate by light irradiation.
Simon Gao: We can see in this picture, this is an original film and light in the transparent portion in this film. For the transparent portion, it is light transmitting where the dry film can receive the light and will react and solidify to form the pattern. Only the transparent part can transmit the light.
Peter Dalmaris: Yes. So, in the parts of the film that are transparent, UV will go through, and that will affect the thin film, which is sensitive to UV light. And that will do what? Would that cause copper to be removed or to stay on the board?
Simon Gao: As we can see from this picture, the dark blue part is the part that has been reacted and received the light. So, this will stay, it remains on the board. And the light blue will be washed away in the next steps.
Peter Dalmaris: Right. So, the UV radiation makes the dark blue parts of the board resistant to the chemical that you'll use later to dissolve the rest. Right?
Simon Gao: Exactly. Here is a video. This is an original. This is our exposure machine. And we apply the original film in the machine. Then, it goes through the process. After this process, we can see the patterns on the dry film. Some circuits, some lines on the circuit boards, actually, it's the dry film. Some parts reacted, some part not.
Simon Gao: Then, it goes through the developing process. Like we discussed, we need to wash away the part of the dry film that has not undergone the light reaction by chemical solutions. And this step is called as developing. The reacted portion will remain on the surface of the board as a resist layer for etching.
Simon Gao: At this step, there are some lines on board, just like we see in the previous video. They are actually not circuits. They're just patterns on the board. To form the circuits, we need to go through the etching process. Look at the yellow line, this is copper. They are complete and not be formed yet.
Simon Gao: Then, we go through the etching to form the circuit. Etching is to remove the unwanted copper, the copper exposed after developing will be etched away by chemical solution to form the inner layer circuit pattern. Then, what we need to do after we form the inner layer circuit pattern, we need to strip the reacted dry film.
Simon Gao: As we can see, the circuit is already formed. But on the top of the circuit, there still remains reacted dry film. So, we need to remove it by stripping process. The purpose is, just like I said, to strip the recessing layer, which is also called reacted layer, dry film layer, that protects the proper surface with a strong chemical to expose the circuit pattern. And the circuit are clear to see, as we can see from the picture. The circuits are clear to see on the board. Let's check a video to better understand it.
Peter Dalmaris: There's quite a few chemicals involved in all of this. It's a chemical process, essentially, from one step to the other.
Simon Gao: Yes. Now, we use Automatic DS line, which combines the development, etching, and stripping process together. We combined the three process together to improve the efficiency of the production.
Simon Gao: At the circuit pattern is formed, we will check it immediately by the AOI machine. The AOI is short for Automated Optical Inspection. It's hard to explain the principle, but I just try. Because the image is fed back to the device for processing by optical reflection principle and compare with the set logic judgment principle or data pattern to find defective position.
Simon Gao: We have stored in this machine the original data from the Gerber files, and we put a board inside the machine and there are several cameras on the index machine to show the picture. We compare the circuit on the picture with the original data to find the differences. And then, we can find the defect parts.
Peter Dalmaris: So, the computer knows what the expected circuit board should look like based on the Gerber files that the client has given you. And then, it uses high-definition camera to see what the actual manufactured board looks like at that point. And if the two don't match, then you get an error report and you can decide whether you should redo the whole thing again.
Peter Dalmaris: Can you correct things once a board has been made? Or do you need to repeat the process if there's a defect?
Simon Gao: Yes. Up to the AOI machine, if we find some defective boards, some small defects, we can compare by our engineer. It can be repaired or fixed.
Peter Dalmaris: But if it's something bigger, you've got to repeat the process, right?
Simon Gao: Yes.
Peter Dalmaris: What is the defect ratio? Like, do you have a number that describes how efficient and reliable the process up to this point is when it goes into the AOI?
Simon Gao: AOI, it's a very effective machine, and within a minute we will find the entire board if it is perfect boards just within a minute. Because we have a large quantity needs every day, so we must have the effective machines in our factories. So, AOI is very common in PCB factories.
Peter Dalmaris: Yeah. That's how it works.
Simon Gao: This is AOI machine, so you can see. The cameras moves very fast in AOI machine, and you can see from the computer within just a few seconds to display where is the defective parts.
Simon Gao: So, after we check the circuits, the next step goes to drilling holes. Drilling through holes that are connected to the lines between the layers and the board surface. Here is also a short video. We have a path board to protect, and also aluminum cover on the top of the board. The purpose is to protect the boards and the circuits.
Simon Gao: So, the next step is to metallizing the holes. Because the holes resin and glass fibres is now conducting, so we need to metallize it to connect the layers. That's the purpose of the hole. And we have two steps to minimize the holes. The first one is PTH, which means the Plated Through Hole. And in this step, we will create a very thin chemical copper layer with a thickness of 20 to 40 microinches, as we can see from the picture.
Peter Dalmaris: How is it done? Trying to imagine it, like, through the process, how do you set the chemical copper layer inside the hole? Because on top of it and below it, it is fine. It's already there. But inside the hole, how do you apply the chemical copper?
Simon Gao: In our next video, it's a large slot and we just put the boards into the chemical solutions, and it's a liquid. It's a liquid, so it will cover every corner of the boards.
Peter Dalmaris: Immersion. Right. So, you dip it into copper then and through immersion, the inside of the holes are plated. Correct?
Simon Gao: Yes. And the second step is panel plating. Panel plating is to plat a thickness of 200 to 500 microinches. You can see from the picture that the copper become -
Peter Dalmaris: Thicker.
Simon Gao: Thicker. Yeah, thicker. Here is a video.
Peter Dalmaris: So, you do that when somebody is installing a component, and paint might be applied, so that can damage the copper if it's too thin. So, you give it a little bit more depth and width.
Simon Gao: Yes. We can see here the chemical solutions we put our boards inside. So, it will cover the holes to get some chemical copper of a required thickness.
Simon Gao: If you are doing a multilayer board, we need also make outer layer in addition to the inner layer. Above the two layers, for example, four layers, six layers, eight layers, we need to go through the outer layer process. But the basic production process of the outer layer is roughly the same as in a layer, so I won't go into details here. The only difference is a tin plating process. The layer of tin is applied to the surface of the platted copper as a protective layer for etching.
Simon Gao: We also need to go through the etching process, so we need to also to protect the platted copper with a layer of tin.
Peter Dalmaris: Do you need to do that in the inner layers? Only the outer layers top and bottom because they're exposed to the elements and you want to protect the copper through that additional step.
Simon Gao: Yeah. Since the other the process of internal circuits have been complicated. And the next steps are all about the appearance. Here, the first is solder mask. Solder mask is a protective layer of the circuit which aims to prevent short circuits and reduce the amount of solder paste during soldering.
Simon Gao: In PCBWay, we have the most choices of solder mask. Apart from the original normal solder mask, red, blue, yellow, we can also find some matte grey, matte black, which is very popular.
Peter Dalmaris: Very popular.
Simon Gao: Yes. Liked by many engineers and makers. And for the solder mask process, we also have many steps, like back in the boards, print front sides, and then back it again, and print the second side. It's also a very complicated process.
Simon Gao: And then, we go to the silkscreen. On the circuit board, we need to add some text or graphics to identify or beautify the boards. We can check this video. In our factory, we use automatic laser printing, which has higher accuracy than the traditional Mandarin printing. In the past decades, we used manual printing. We used a hand and the cover of the -
Peter Dalmaris: Like you do a t-shirt.
Simon Gao: Yes. Like a t-shirt. Nowadays, we use the automatic machine to replace that.
Peter Dalmaris: So, is it a laser printer you said that does this?
Simon Gao: Yes. Laser printing.
Peter Dalmaris: Right. It's very high definition then and very accurate. It can print really tiny things and the graphics turn out amazing these days.
Simon Gao: Yes. And the next step is a surface finish. Sometimes some makers or clients - because I deal with issues with clients - just ask me why we need the surface finish. "Can I cancel this choice?" It's very interesting as you can find on the website. We do have the no choice, that means we will not do this if it's finished for your board. But it costs much higher than you do because it's all normal.
Simon Gao: Why we use the surface finish? Because if the bare boards has been exposed to the air for a long time, it will be easily oxidized by moisture. It's unlikely to remain original copper for a long time, so we need to paste a productive layer to protect the copper, the paths on the board to stay a longer time.
Peter Dalmaris: I see. So, the problem here is not what is in this picture covered by the green chemical, that's protected. It's the exposed copper that is the problem and that needs its own protective layer but it still needs to be conductive. And that's what you're talking about here, right?
Simon Gao: Yes.
Peter Dalmaris: Yeah. So, if they saw these options there, I guess, the bottom ones seem to be very expensive, hard gold. Who would use hard gold?
Simon Gao: We have multiple choice to meet the different needs from customers. Then, we go to the outline process. We need to cut the boards into the size required by the customers. In a first step, we combine the different designs into a large panel. In the last step, we need to separate the boards into pieces. For panelised boards, we use V-scoring or tap routing to make some slots on the board, so it will be easier for the customers to split the panels into pieces after assembling the boards.
Simon Gao: Sometimes we assemble the boards because it were easier for us to do assembly. It were more efficient to do assembly for a large panel, especially for the small boards, we need to panelise them together.
Peter Dalmaris: So, there's a drill there involved that will detect their appropriate patterns, I suppose. It needs to cut into the board with the drill. And then, there's a worker that will snap them into the individual boards from the panel. There's a hammer there. With the hammer, you're securing it on the table so that the machine can go ahead and do the cutting, [inaudible].
Simon Gao: Yes. After we mil the boards or cut the boards, we need to clean the boards in a final step. Because there are some contaminates on the boards. Then, it goes to the final step, quality control. The bare boards test is performed according to the requirements of electrical performance. Normally, we use flying probe test to check if there is any shorts or open circuits to ensure the electricity of the board.
Simon Gao: And we can also offer function tests according to the client's needs. Sometimes the clients just ask us, "Do you offer function tests? Can you program the boards?" We say yes, but you better to provide us the methods or the fixture so we can actually do it.
Simon Gao: And after we've checked the circuits and the function, we will go to the final check inspection, visual inspection to check if there is any defects of appearance. And, also, to [inaudible] the boards to the required quantity. And then, back to the board together.
Peter Dalmaris: And then, off to the customer.
Simon Gao: Yes. And this is a line probe test, it moves very fast to test every path connects on the board. And here is also an automatic testing machine. It goes faster than flying probe test machine.
Peter Dalmaris: Yeah. Yeah. This tests, on an individual board, it tests every trace to make sure that it's continuous and there's no cuts. I guess, something that you've already tested optically earlier, but since you did the AOI, a few other things have happened. So, now, you check again to make sure that there's no breakages in the tracers in particular.
Simon Gao: Yes. Yeah. Until now, the whole PCB manufacturing process has been complete. But when you know well about PCB manufacturing process, you will have a better understanding of why it is sometimes expensive to get a PCB produced. Because it will go through many, many processes, and it's not easier for the manufacturer to keep the lower price. But, you know, the price is still very low nowadays.
Peter Dalmaris: Compared to what it used to be, absolutely.
Simon Gao: Yes. So, many clients ask me, "Is there any way to make the price lower?" sometimes when placing a PCB order. I would always offer some suggestions according to their designs. I also prepare some tips for you, for everyone to read.
Peter Dalmaris: Great. I wanted to ask you about that.
Simon Gao: We just said how to reduce price. I collected four tips to reduce the PCB cost. The first one, dimension. The first factor, of course, because the dimension really matters on the PCB price. A lot of manufacturers, including PCBWay, gives a special offer under certain conditions where the size is mentioned as a key constraint.
Simon Gao: I'd like to suggest to you to try your best to make the dimensions within 100 and 100 millimetres because it will, of course, reduce the price directly. No matter what layers of your board try to reduce the material, the costs will also be reduced. But don't just pursue small sizes and sacrifice the whole diameters and spacing. If you reduce the whole diameters and spacing at the same time in order to get the board smaller, it is likely to get more expensive.
Simon Gao: Another point you need to be aware of is the shape. A wide irregular shape, because the irregular shaped borders are very likely to be damaged during cutting process. As you can see from the picture, there's some corners, some very small parts of the board. When we mil in the boards, it's likely to damage the board. So, we need to prepare more material to build this board in order to meet the quantities. So, that also costs more because the higher price reason.
Peter Dalmaris: Yeah. Rectangular PCB then seem to be best because the sizes are regular, easier to handle, snap off apart from the rest of the boards and the panel, so less waste, therefore the price is lower.
Simon Gao: Yes. But most of the time, actually, if the makers want the irregular shaped boards, they have specific purpose of it. Maybe that's their design. That's a map of their country, sometimes. So, they, of course, don't want to change it. It doesn't matter.
Peter Dalmaris: You can still do it.
Simon Gao: Yes. And the next factor is vias. The vias comes in three tabs, through hole vias, buried vias, blind vias. Through hole vias are drilled all the way through the board. Where a blind vias goes in the middle. By using through hose vias as much as possible, rather than blind vias or buried vias layers, because the production becomes more complicated to use HDI technology, that means high density technology.
Simon Gao: Bigger hole diameters are preferable during PCB manufacturing as they require less precision. Smaller holes means you need more control in precision to achieve. These factors demands specific equipment that will in turn drive the production costs higher. As the hole size, I mean, the diameters of the hole, I would recommend you to design it larger than 0.3 mm, the price will be reduced.
Simon Gao: And same as the hole size, it's better to make sure that trace spacing all above 6mils unless you have specific purpose of the design. When we keep the min hole size, as we can find the chart on the left, when we keep the min. hole size unchanged, 0.3 mm. And keep reduce min trace spacing, six, five, four, three, the price goes [inaudible].
Peter Dalmaris: Makes a big difference.
Simon Gao: Increased a lot. And when you have the smallest hole in the design, then you don't need to worry about the trace, because it would do nothing with the price. So, we can know that the hole size has great impact on the price than circuit trace spacing. So, care most about your hole size.
Peter Dalmaris: You hole size than the tracks. It's a big difference.
Simon Gao: Yeah. The last one is panelise your tiny boards. If you need a large amount of tiny PCBs, it's better to panelise them into a big panel. It's not only very easy for assembly process, but also can be very cost effective. But I don't suggest you to panelise several different designs in big panels boards, because if the quantity is more, this will lead us to use the actual original film, dry film, and cost more.
Peter Dalmaris: So, what you're saying is, if I want to manufacture multiple boards that could take up a whole panel, then I can panelise my small PCBs to fill a full panel. And I can do that when I submit my project to you, so you can skip that step, and just take up a whole panel for my single multiple design, right?
Simon Gao: Yes. And a tiny PCB with a large quantity, we suggest you panelise your boards. And you have different designs in a big panel if the quantity is small, I mean under ten pieces. Some projects have orders. We don't suggest you do so because every different extra design, we need extra, about, $12 each design.
Peter Dalmaris: If we panelise it, even though it doesn't take up a whole panel at your end. You still need to use a film and probably do additional work to make it fit with other designs as well.
Simon Gao: Yes. And I also suggest you to notice that the measures we have mentioned above are based on not changing the performance of your products. Just try to avoid unnecessary special designs in a board that will reduce your cost, that's my point.
Peter Dalmaris: Do you need any special provision or instructions from your customers if they have some functional components of the design that are part of the PCB? Like, I'm thinking here antennas, for example, for Bluetooth or Wi-Fi that are integrated into the PCB these days, is this something that you need to know about as a manufacturer or nothing special for you?
Simon Gao: For the assembly process, yes, we would better to know the component's suppliers. Yes, it will be easier for us to understand the boards and to exactly control the production of the boards.
Peter Dalmaris: So, in the ordering process, I believe you have a field where the customer can type in information such as "Beware, there is an antenna on my design," so that your engineers can read that and then take that into account when they inspect the board.
Simon Gao: Yes. We do have a part on the Instant Quote page so clients can send a note to our service representation.
Peter Dalmaris: Yeah. Great. So, you've given us your key learnings from your presentation, which are, I guess, easy to remember methods to reduce the total cost of manufacturing PCBs, which I think do make a big difference. You showed us how standardizing the drill size for a hole, 0.3 mm makes a huge difference in the pricing of the board. So, things like that are very important
Simon Gao: Now, for those of us who'd like to learn more about the manufacturing process of PCB, the rules that we need to keep in mind when we are designing our PCBs in whichever CAD application we're using, do you have some suggested resources that we can have a look at?
Simon Gao: Yes. In my presentation today, I referred to several videos here, you can find more detailed information in the following videos. Apart from the PCB manufacturing process video, you can also check our assembly process and factories in the videos.
Peter Dalmaris: Great. We'll include those links in the presentation page so we can just click on. I think the PCBWay website also has a lot of documentation on the design rules that you can learn from and then import them into your CAD design tool. So that when you are working on a PCB, the design tool itself can apply those rules and make sure that your PCB design complies, and you don't go beyond the capabilities of the manufacturer. Any specific pages that you want to point out on the website for documentation especially?
Simon Gao: Here are some pages that the users can refer to in our website and capabilities page. And instant quotes, also community, to ensure your products and others projects.
Peter Dalmaris: It's a sharing page, you can share your open-source hardware designs with other people, and you can use other people's designs.
Simon Gao: Yes. And if you have any interest in cooperating and also student sponsorship queries, you can drop off a message to me by this email, [email protected].
Peter Dalmaris: Great. Thank you. I was about to ask you about contacts. There you go. That's great. Thank you, Simon. It was an excellent presentation. It's really given me a lot of clarity about what happens behind the scenes, like when I receive those beautiful PCBs back, I see the end result. And it's hard to imagine how much work goes in providing that and how many people have to work in that production line to make it happen. It takes just a few days, but it's complicated. It's a lot of technology, big machines, [inaudible].
Simon Gao: I hope it helps. Yes. I hope it helps.
Peter Dalmaris: It definitely does. So, again, thank you very much and I'm wishing you a good day.
Simon Gao: Thank you.
Get life time access to all Maker Mind-Meld masterclasses
Watch each masterclass from the comfort of your own home and learn about their tools, techniques, and thinking processes so that you can become the best maker you can be, at your own pace.
Get audio downloads of all 22 session, the Maker Mind Meld "Playbook" session notes.
Jump to another article
1. Silke Bethke, John Nyagah And Catherine Squire Blatti: Supporting Families Of Young Children Through STEM Education
2. Dr Peter Ellerton: Critical Thinking In STEM
3. Celinda Corsini: Am I Teaching Robots Or Humans?
4. Prof John Fischetti: Co-Constructing The Learning Journey With Our Children
5. Dr Ken Dovey: Leadership In Education, A Collective Achievement
6. Seven Vinton: Strategies For Extending Student Logical Reasoning
7. Alain Pannetrat – Building A Wired IoT Platform For Makers
8. Karsten Schulz – Making A Computer Processor With The B4 Kit
9. John Teel – 15 Steps To Develop Your New Electronic Hardware Product
10. Jordan Christman – Getting Started With FPGAs
11. Nicola O’Brien: Remote learning now and in the future
12. Dal Gemmell – Telcos Aren’t The Future. You Are.
Last Updated 3 years ago.
We publish fresh content each week. Read how-to's on Arduino, ESP32, KiCad, Node-RED, drones and more. Listen to interviews. Learn about new tech with our comprehensive reviews. Get discount offers for our courses and books. Interact with our community. One email per week, no spam; unsubscribe at any time