KiCad 6 Guide series
PCB Key Terms
This article will teach you the most commonly used terms for understanding information found on PCB fabrication websites and CAD tool documentation.
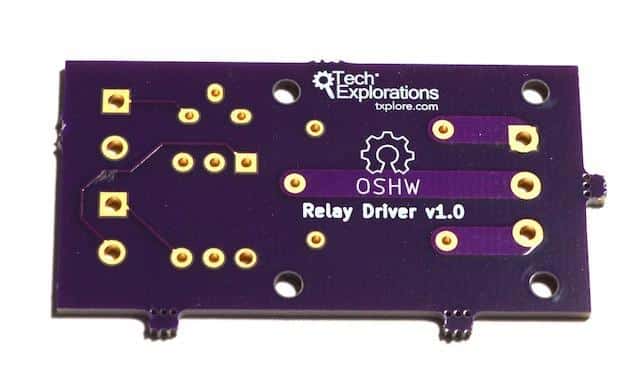
Creating printed circuit boards is an engineering discipline. As such, it has its own 'language.' In this article, you will learn the most commonly used terms to understand the information found in places such as PCB fabrication websites and CAD tool documentation.
FR4
The most common material used to make printed circuit boards is FR4 (or FR-4). It is a glass-reinforced epoxy laminate composite material, or in simpler terms, fiberglass cloth bound using an epoxy resin.
Go over to the Wikipedia article to read more about this material.
The 'FR' part of the name stands for 'Flame Retardant,' a desirable quality for a board that will hold together components that can potentially ignite when they fail.
Other valuable attributes of the FR4 substrate are:
- Very light and strong
- Does not absorb water
- It is an excellent isolator
- Maintains its quality in dry and humid environments
Other materials can be used in rigid or flexible printed circuit boards, apart from the standard FR4 and variants (like FR4 tracking resistant and halogen-free). Examples include G-11 for applications that must operate in high temperatures, FR-3 (cotton-paper impregnated with epoxy), and Polyimide (high-performance yet expensive, appropriate for cryogenic applications).
Traces
Traces (also called 'tracks') are conductive paths. Most often, the material used to make traces is copper. Electrical signals and power use traces to travel throughout a circuit.
In Figure 5.3.2.1, you can see the traces in the front side of this PCB as thin purple lines that provide the connections between the golden pads where the component terminals will eventually be. You will learn more about pads later.
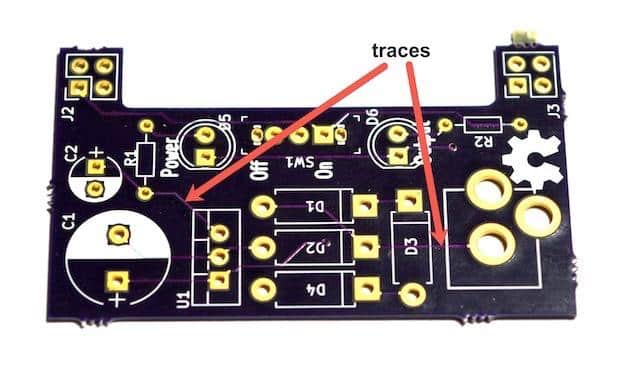
Figure 5.3.2.1: An example of traces.
As the designer of a PCB, you have total control over the characteristics of traces. You can control their width, height, and route, including the angles by which a trace changes direction. If you want a trace to accommodate a large current flowing through it with little resistance and temperature rise, you can design it wider and thicker. This is useful when a trace must feed power to the components of your board. Traces that convey low power-current signals (less than 20 mA) can be narrower using less copper.
Keeping the width of traces to around 0.3 mm (or even less, depending on your manufacturer's guidelines) makes it possible to draw traces closer together and reduce the final size of your PCB.
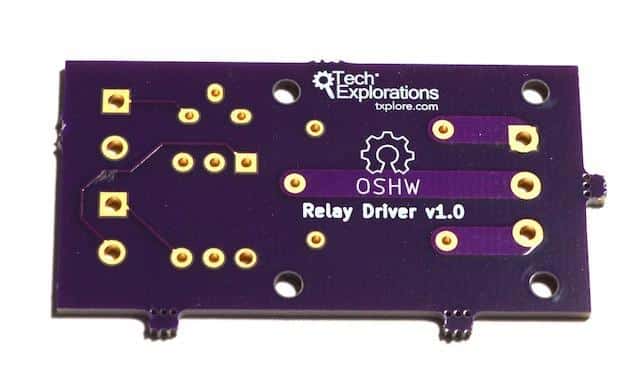
Figure 5.3.2.2: An example of wide traces.
In Figure 5.3.2.2, you can see an example of much wider traces than regular signal traces. These traces connect the terminals of a 240 Volt relay.
The traces in these examples are purple because of the solder mask chemical used to finish the manufacturing process. You will learn about the solder mask further down in this article.
Pads and holes
Pads and holes are the most prominent feature of a printed circuit board. Pads come in two varieties: TH (through-hole) and SMD (surface-mounted device). For each, there are several shapes.
In Figure 5.3.3.1, you can see an example of a board that contains TH pads exclusively, and in Figure 5.3.3.2, you can see a board with TH and SMD pads.
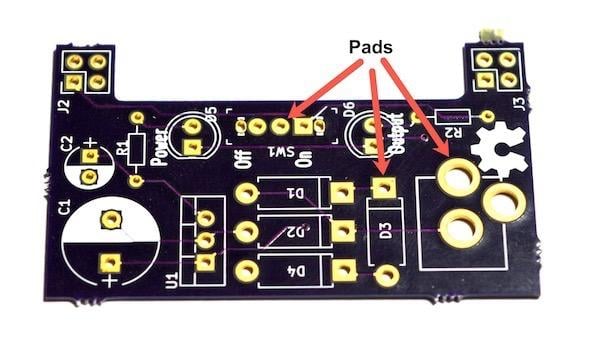
Figure 5.3.3.1: Through-hole pads.
Through-hole pads, unlike SMD pads, connect the front for the PCB with the back electrically. In the examples, you can see that the gold plating of the pad fills the inside of the hole. If you turn the PCB around, you will see that a matching pad exists in the back.
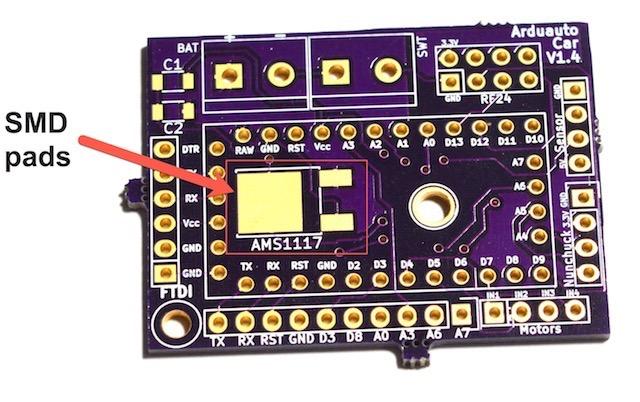
Figure 5.3.3.2: An example of SMD pads.
Boards with mostly TH pads are popular among hobbyists because through-hole components are easier to work with, at least initially. SMD components are smaller; hobbyists tend not to use them until they are more comfortable with their soldering skills. With a bit of practice, SMD components are as easy to work with as their TH counterparts.
In the industry, on the other hand, the vast majority of PCBs are designed to contain SMD components. This is because SMD components can be populated automatically using pick and place machines and because their small size results in smaller PCBs.
Apart from the two varieties I described above, pads also come in several shapes. Most often, you will see round pads, but rectangular and oval shapes are also possible. Using KiCad, you can create such pads and control their geometry to the extent that your PCB manufacturer allows.
In Figure 5.3.3.3, you can see an illustration of a cross-section of a PCB showing the configuration of pads, and two types of holes, Plated-Through Hole (PTH) and Non-Plated Through Hole (NPTH).
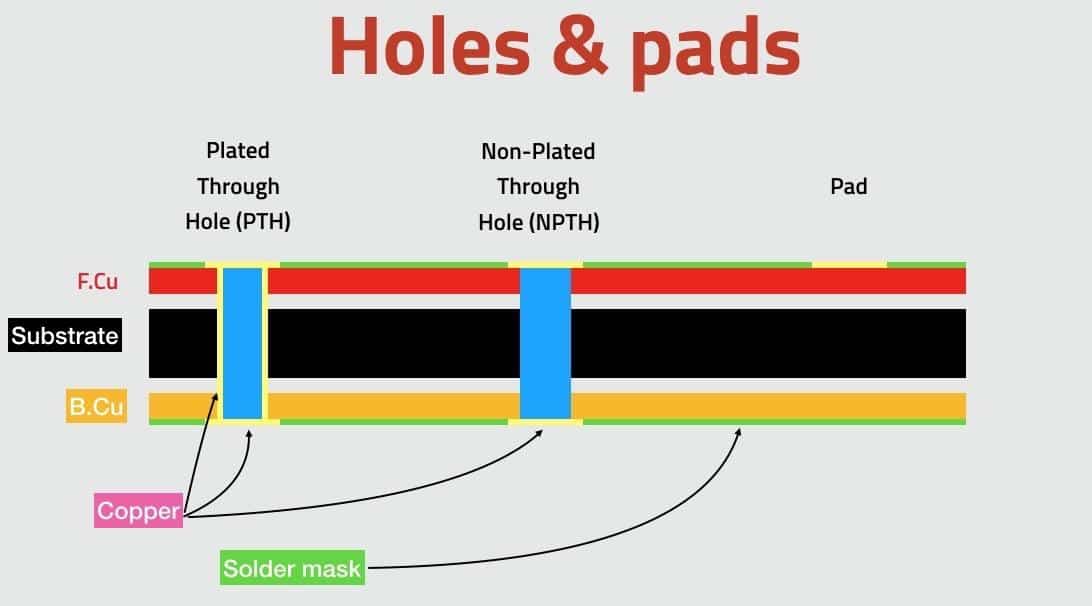
Figure 5.3.3.2: An example of SMD pads.
Plated-Through Holes is the more common variety and the default type of hole in more cases. We use a drill to create the hole and then copper to cover the hole's sides so that its two ends (at the front and back copper layers) are electrically connected. Vias are constructed the same way, except they have a smaller diameter, so it is impossible to accommodate component pins.
On the other hand, in a Non-Plated Through Hole, we use the same drill to create the hole, but no copper is used to cover the sides of the hole, so there is no electrical connection between its two ends.
Finally, pads without holes are useful for attaching surface-mounted components, as you learned earlier.
Via
You can create a via when you want to move a signal that travels across a trace from one side of a PCB to another (say, from front to back). A via is a hole with its sides covered with copper or gold (or other conductive material) that allows a trace to continue its route across layers.
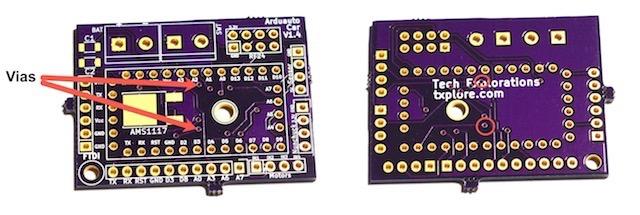
Figure 5.3.4.1: Vias allow a trace to continue between layers.
In Figure 5.3.4.1, you can see the two sides of the same PCB. On the left, the arrows point to two vias in the front of the PCB, and on the right, the circles indicate the same vias on the back of the PCB. Vias are similar to through-hole pads, except they don't have any exposed copper (the solder mask covers them), and they don't have a pad (so you can't solder a component).
In simple circuits with only a few components, it is possible to create all traces on one layer of the PCB. When a PCB gets busy with more components, it quickly becomes impossible to do the routing on a single layer. When multiple layers are needed, vias provide the simplest method of allowing a trace to use the available board real estate.
In Figure 5.3.4.2, you can see the types of interconnections between layers that are possible.
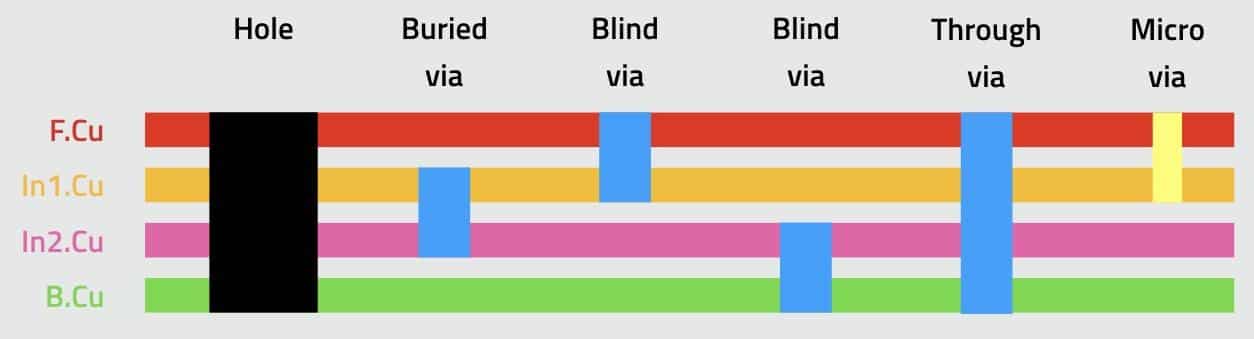
Figure 5.3.4.2: Types of interconnections between layers.
For through-hole components, you would design a hole that connects the top and bottom copper layers. We use a drill to create this hole. It is wide enough to allow for the pin of the component to go through it.
In vias, the diameter is smaller when compared to a regular platted hole. They are not wide enough for pins to go through them, but they are plated, like holes, and allow for electrical connection between layers.
A 'through via' is like a hole but narrower. It connects the top and bottom layers. A buried via is a via that connects any two internal layers. In the four-layer example of Figure 5.3.4.2, the buried via connects the In1.Cu and In2.Cu. A 'blind via' also connects two layers but has one end exposed to the outside of the board, either top or bottom.
Another option for interconnecting layers in high-density boards is to use a 'micro via' ('uvia'). A micro via is made using a high-powered laser instead of a mechanical drill; the use of lasers makes it possible to reduce the diameter of the via dramatically .
Annular ring
The annular ring is a term that describes the area on a pad that surrounds a via. A primary metric of an annular ring is its width, defined as the minimum distance between the edge of the pad and the edge of the via or pad hole.
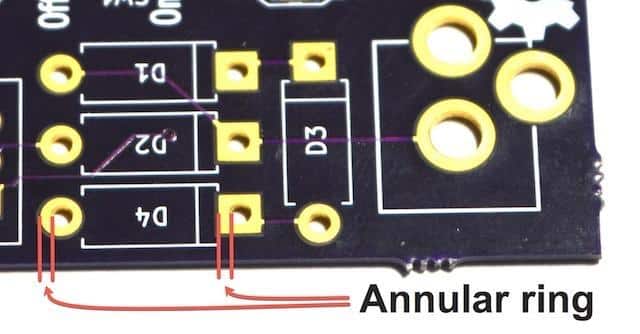
Figure 5.3.5.1: Annular rings and width.
In Figure 5.3.5.1, the width of two annular rings is marked with two red lines. Ideally, the drill hit (the location on the board where the drill lands and creates a hole) is in the middle of the pad. If the drill bit is not aligned correctly, the hole can be closer to one edge of the pad (a 'tangency'), or it could even miss the pad completely (a 'breakout').
Soldermask
As you know, traces are made of copper. Copper slowly reacts with oxygen in the air, resulting in oxidization. Oxidized copper produces a pale green outer layer. PCB manufacturers cover the exposed copper with a solder mask, a thin layer of polymer that insulates it from oxygen to prevent this from happening. As an additional benefit, the solder mask also prevents solder bridges from forming between pads.
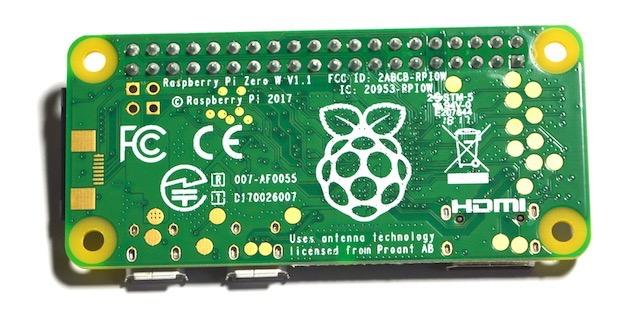
Figure 5.3.6.1: The rear of a Raspberry Pi Zero is protected by a thin layer of solder mask.
In Figure 5.3.6.1, you can see the back of a Raspberry Pi Zero. In this example, the copper is protected by a thin layer of green solder mask. Only the pads and the mounting holes are not covered by the solder mask.
Solder mask polymers are available in different colors, with green being the most common and cheaper. You can create fancy-looking PCBs with black, blue, red, purple, and many other colors.
Silkscreen
Printed circuit boards are not complete without text and artwork. The purpose of those elements is to convey useful information and add a touch of elegance. In Figure 5.3.7.1, you can see an example of such text and artwork on the back of a Raspberry Pi Zero. You can see the Raspberry Pi logo, logos of various certifications, and different text items that inform us about the model, etc. All this consists of the silkscreen.
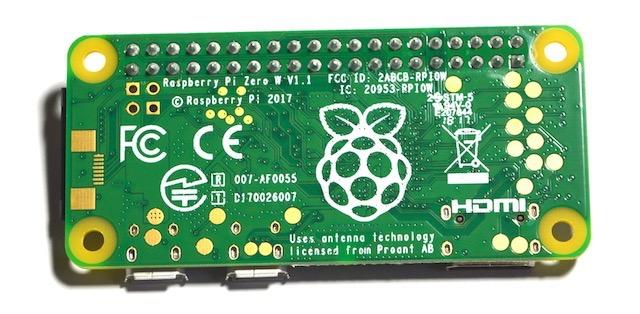
Figure 5.3.7.1: The
The name 'silkscreen' is somewhat misleading. Of course, no natural silk is used to produce the white elements on the PCB. The method used to print the silkscreen in large numbers is a relative of the traditional screen printing process that you can use to print a graphic on a T-shirt. The silkscreen text and graphics are printed on the boards while they are still in their panels.
White is the most common color for the silkscreen, but black and yellow are also available.
In the projects that you will work through during the KiCad Like a Pro 3e course or eBook, you will spend a considerable amount of time creating the informational and decorative text and graphics in the silkscreen layer of the PCB.
Drill bit and drill hit
Drill bits are used to create holes and vias, but also cutouts. Drill bits are typically made of solid coated tungsten carbide material and come in many sizes, like 0.3 mm, 0.6 mm, and 1.2 mm. They look like the one in Figure 5.3.8.1. These drills are attached to computer-controlled drilling machines and are guided by a file that contains information about the coordinates and the drill size for each hole on the PCB.
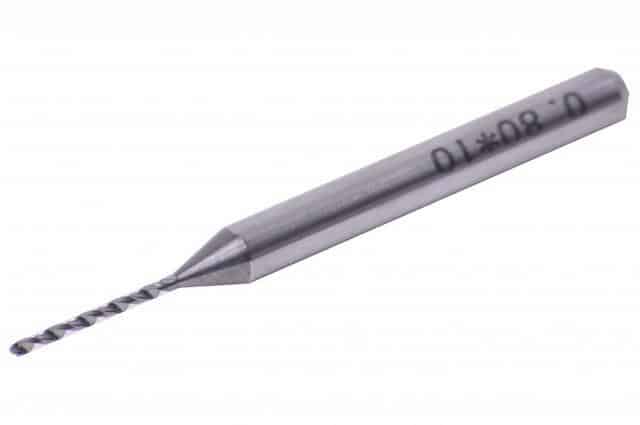
Figure 5.3.8.1: A drill bit.
It is interesting to note that drill bits are replaced with lasers for tiny holes, like vias. These vias are often called 'micro vias. With laser drilling, it is also possible to create vias that connect in-between layers of the PCB.
The term 'drill hit' describes the location on the PCB where the drill bit comes in contact with the PCB and creates a hole.
Surface mounted devices
If your objective is to create a PCB that is easy to manufacture in large numbers, with a minimum size, you should design it to contain surface-mounted components instead of through-hole components.
In Figure 5.3.9.1, you can see an example of what is possible to do with SMD on PCB. A computer, on a tiny board, for a few dollars.
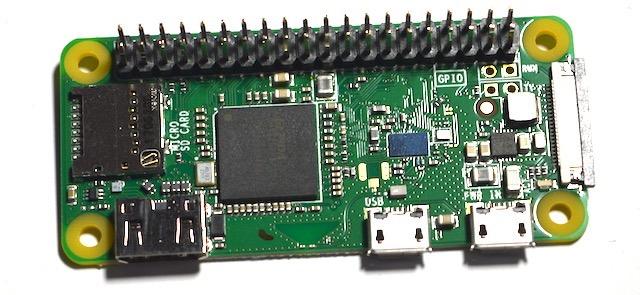
Figure 5.3.9.1: The Raspberry Pi Zero contains almost exclusively SMD components.
On this board are a highly integrated microprocessor, memory, communications, and connectors. Even the connectors are SMD. The only through-hole component is the pin header.
Creating something like this using through-hole components, if at all possible, would result in a board that was many times the size of the Raspberry Pi Zero and would cost many times more because most of the assembly would have to be done by hand.
While hobbyists prefer to work with TH components because they are easier to solder and repair, learning to work with SMD, at least the larger ones, is certainly possible.
In the KiCad Like a Pro 3e course and eBook, you will learn how to create an SMD version of a PCB, in addition to the TH version.
Gold Fingers
Appropriately called 'Gold fingers' are gold-plated connectors placed on the edge of a PCB. Gold fingers are useful for interconnecting one board to another. You can see an example in Figure 5.3.10.1; it shows the micro:bit educational single board computer.
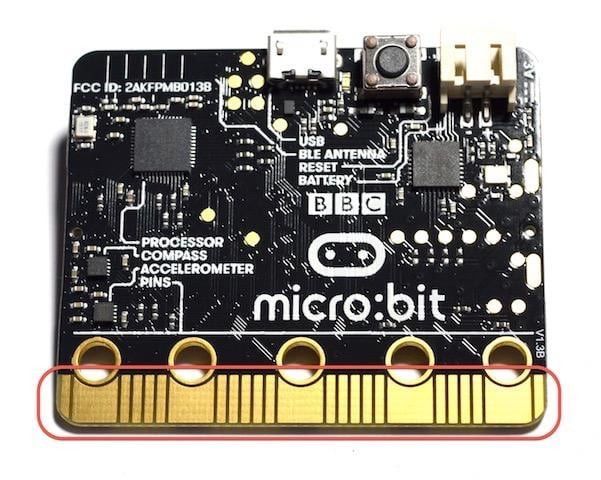
Figure 5.3.10.1: Gold fingers on a Micro:bit.
The micro:bit uses gold fingers to connect to other devices via a slot, like motor controllers and sensors. Gold fingers make it possible to attach and detach the PCB to a slot at least 1,000 times before they start to wear out.
Keep-out areas
A “keep out area” is what it sounds like: an area on the PCB that must be clear of components and perhaps even traces.
In Figure 5.3.11.1 I show three examples of devices that contain keep out areas.
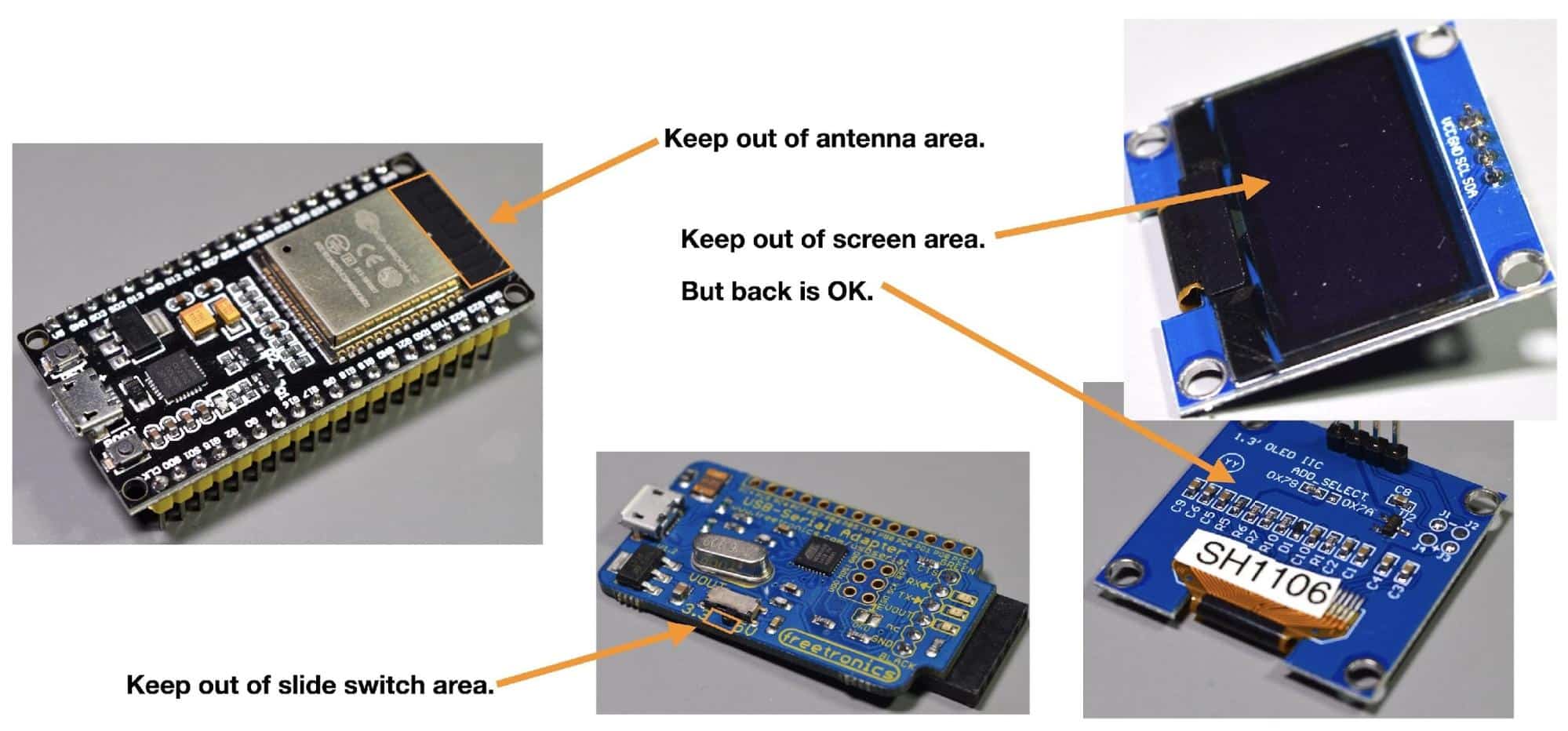
Figure 5.3.11.1: Examples of devices that contain keep out areas
CAD software, including KiCad, allows you to mark an area on the PCB as “keep-out.” In KiCad, you can also configure the keep-out area to prevent the user from adding specific or all types of elements, including footprints, tracks, vias, and cutouts. You can also tell KiCad to apply the keep-out rules to specific (or all) copper layers.
On the top left is an ESP32 development kit. The kit is based on an ESP32 module that contains an integrated antenna that requires a patch of PCB clear of components and other traces. You don’t want to add any other components in that area not to affect the antenna’s performance. Note that the keep-out area must include all copper layers, not just the front one where the antenna is.
On the right side of Figure 5.3.11.1, I show the back and front sides of a TFT screen that I use in my Arduino projects. The front side is where the TFT screen is placed. You can see that the screen’s ribbon connector is attached to a row of pads in the back of the PCB. We can mark a keep-out area in the front of the PCB only and allow for footprints and traces to be placed on the back of the PCB.
The last example, in the middle of Figure 5.3.11.1, is a UART interface with a voltage slide switch. The slide switch is oriented to its side. Even though the switch notch is tiny, it is still a good idea to mark the area below it as a keep-out area for footprints but allow traces. This way, there is no risk of placing a footprint by mistake and obstructing the travel path of the notch. However, we can still use that patch of PCB for tracks or vias.
With KiCad, you can create keep-out areas of any shape and configure them in almost any way needed.
Panel
To manufacture PCBs economically, manufacturers use machines that can work on large panels. Each panel can contain many copies of the same PCB. It is also possible to use clever algorithms that place different PCBs on the same panel so that the panel's capacity is fully utilized and that the individual cost of each PCB is reduced. This is how it is possible to have a single 'hobby' PCB manufactured for a few dollars. This panelization process is key to this reduction in costs.
In the example of Figure 5.3.12.1, a single panel contains four individual PCBs. The four PCBs are populated while still part of the panel using an automated pick and place machine. A pick and place machine is a robot that uses an arm to pick each component from a container and places it precisely on the pads. Once the components are on the board, the panel moves into the next step of the process, in which they are 'baked' and secured in place.
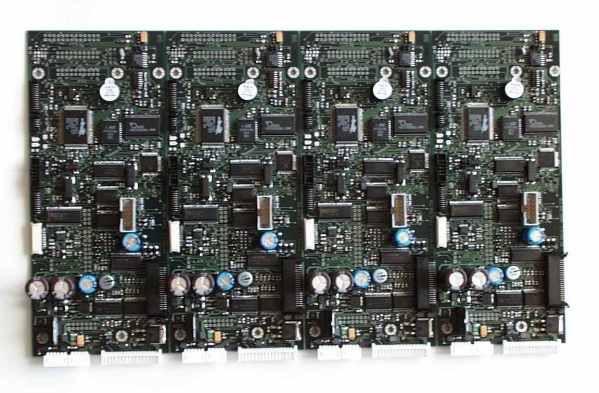
Figure 5.3.12.1: A panel with four individual PCBs.
Manufacturers utilize defined breakaway routes and points on the board to remove the PCBs from the panel to snap them off. In Figure 5.3.12.1, you can see the breakpoints along the edges of this PCB.
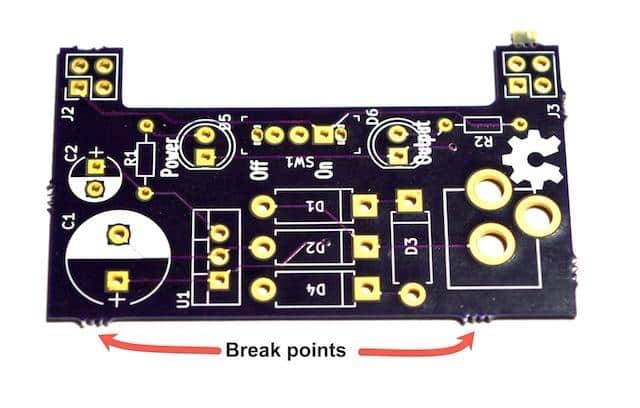
Figure 5.3.12.1: This PCB was part of a panel.
Using a drill, the manufacturer removed the substrate material in between the breakpoints. With a small amount of force, you can remove individual PCBs from the panel without damage.
Solder paste and paste stencil
Solder paste (or solder cream) is a soft and sticky material (at room temperature) applied on pads. The purpose of solder paste is to help attach an SMD component to the pad. Think of solder paste as ordinary solder. With solder, you will need a soldering iron to heat it, melt it, and apply it on a component pin already in place. With solder paste, you will first use a syringe (or one of the other application methods) to cover the pad, then place the component on the pad, and provide heat in the form of an oven to heat the paste and bond it with the pad and the component's plated area.
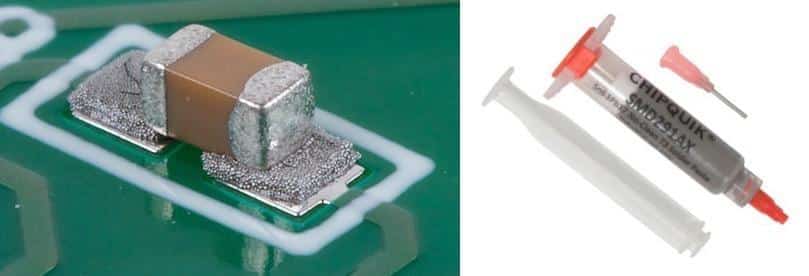
Figure 5.3.13.2: Solder paste in a syringe dispenser and an SMD component.
In Figure 5.3.13.2, you can see an example of a solder paste in a syringe dispenser that you can purchase from retailers like RS Components. Using the syringe equipped with a thin nozzle, you can manually deposit a small amount of solder paste on the pads. Using tweezers, you can place the component you want to attach on the solder paste. Because solder paste is sticky (before it's baked), the component will adhere to it. After you have all the components you want on the board, you place the board in an oven to bake it. After the baking process is complete, the solder paste becomes solid. The SMD components will be mechanically secure and electrically connected to the pads.
Solder paste also comes in a tub, which is more appropriate for application to a board using a stencil (Figure 5.3.13.3). Stencils are helpful in large-scale productions.
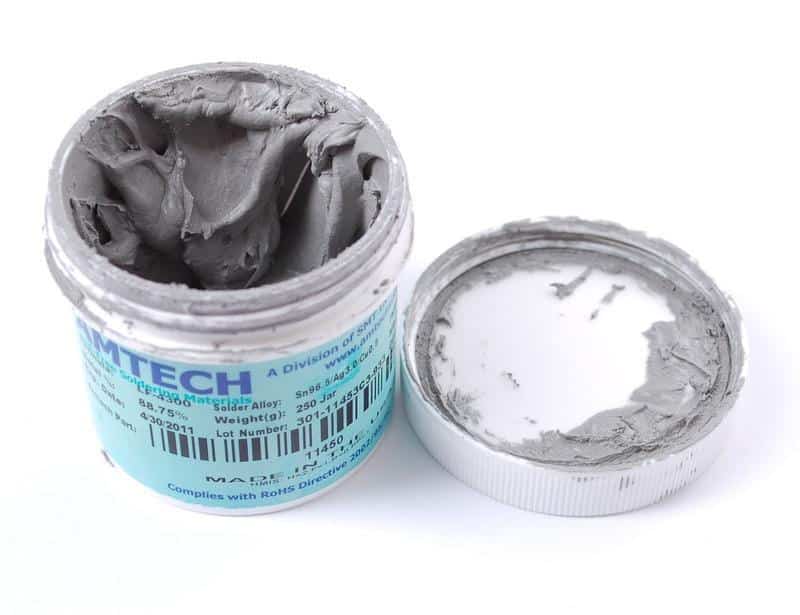
Figure 5.3.13.3: Solder paste is a tub container.
A stencil, typically made of stainless steel, is cut to have openings of the exact size and the precise location of the board's pads. The technician will place the stencil over the board and then apply the paste to the openings. When the technician removes the stencil, the paste remains on the pads only.
Then, manually or using an automated pick and place machine, the components are placed on the pads and stick on them because of the paste. The last step is to bake the board in a reflow oven to solidify the paste.
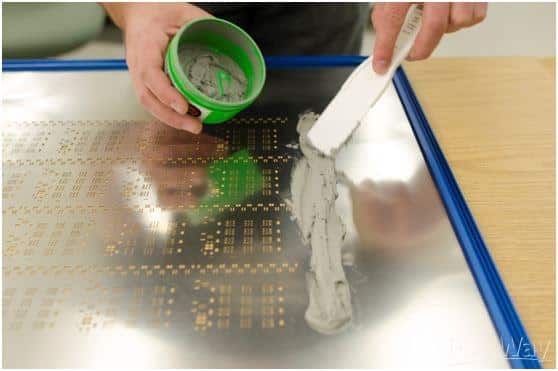
Figure 5.3.13.4: A stencil, with solder paste being applied using a squeegee (photo courtesy of Pcbnew.com).
A reflow oven is an industrial-sized machine used to complete attaching SMD components on a PCB. You can also purchase or make a reflow oven for use at home. People have even made reflow ovens for their projects using discarded toaster ovens. In either case, a reflow oven is designed to operate under a specific program that controls the amount of heat a board receives over time. This is important because the heat must be appropriate for converting the solder paste into good-quality electrical connections without causing damage to the board or the components on it.
Pick-and-place
Pick and place machines are robots that assemble the various components on the surface of a circuit board. When you contract a manufacturer to make your boards and populate them, they will be using a pick and place machine. You can see an example of a pick and place machine in Figure 5.3.14.1.
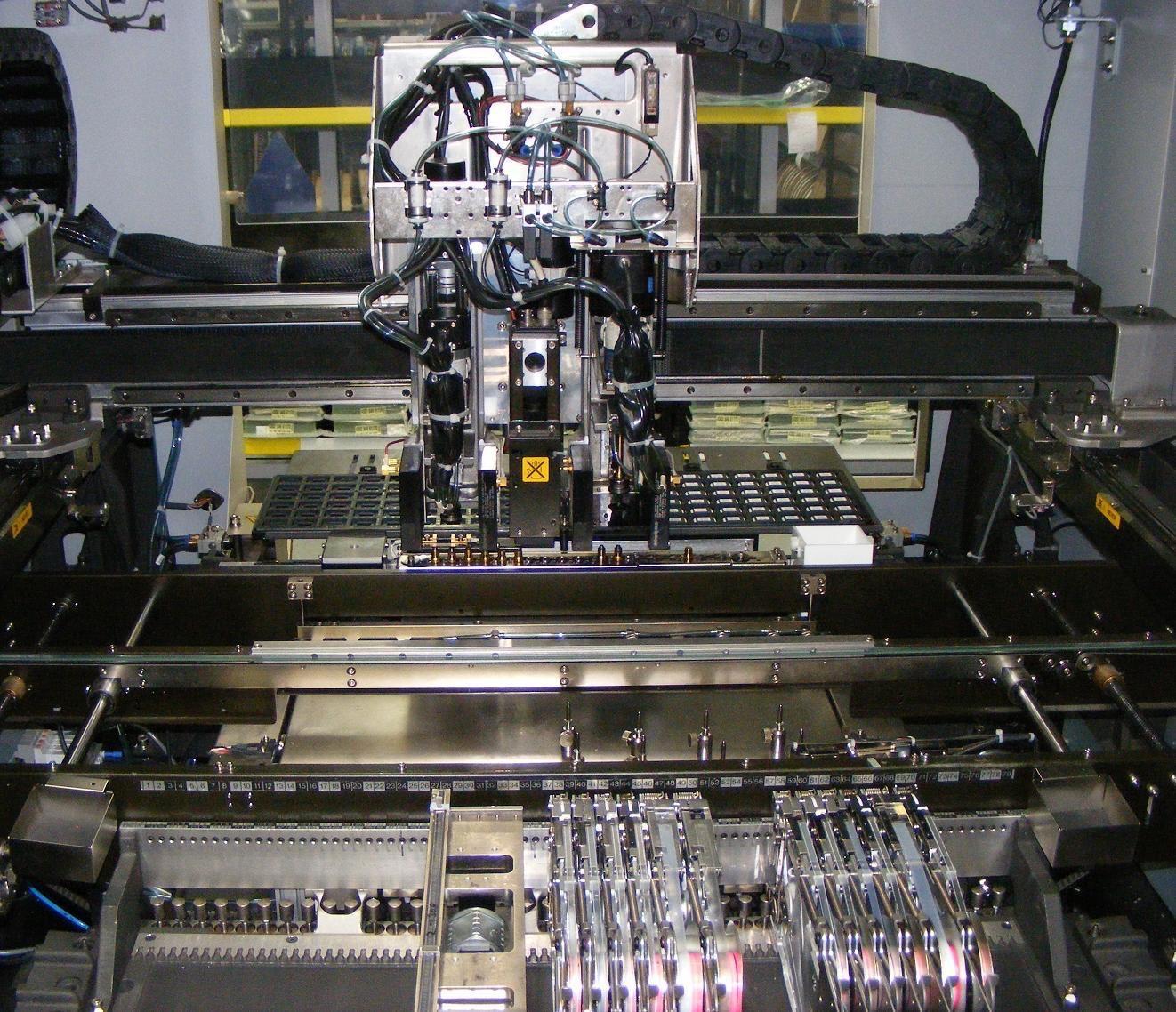
Figure 5.3.14.1: Figure 12.18: A large pick and place machine. By Peripitus [GFDL (http://www.gnu.org/copyleft/fdl.html) or CC BY-SA 3.0 (https://creativecommons.org/licenses/by-sa/3.0)], from Wikimedia Commons
A typical pick and place machine, like the one in Figure 12.18, includes:
- A repository of the various components that are to be placed on the board
- A conveyor belt that brings in the boards.
- An inspection system composed of cameras that can optically recognize the board, components, and other guidance markings on the board.
- A robotic arm that can pick a component from the repository and place it on the board (these arms are usually fitted with suction cups so they can pick and manipulate components).
Modern high-end machines are very versatile, optimized for short runs of complicated boards that employ artificial intelligence. These machines are designed to assemble and test boards autonomously, ensuring high levels of reliability.
Ready to learn KiCad?
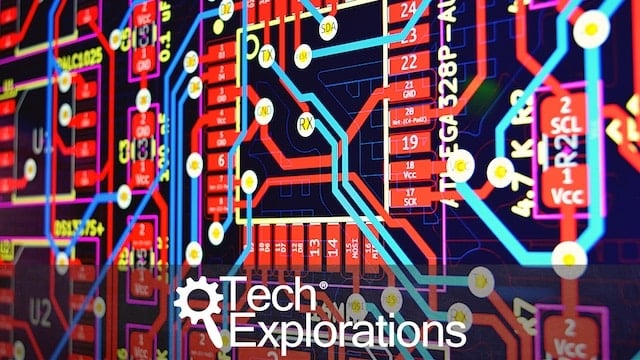
Learn the world's favourite open-source PCB design tool with the world's most comprehensive course
KiCad Like a Pro, 3rd edition is available as a video course or as an eBook.
Choose the version that fits best with your style of learning, or get both to get the full benefit of the video demos plus the details of the eBook.
When you complete KiCad Like a Pro 3e, you'll be able to use KiCad to design and manufacture multi-layer PCBs with highly integrated components and a professional-looking finish.
Work through five projects that give many opportunities to learn and practice all of KiCad's important features.
KiCad Like a Pro 3e contains full sections dedicated to PCB and design principles and concepts. These ensure that you will master the fundamentals so that your PCB project are awesome.
If you are someone who is interested in designing PCBs using KiCad, or moving to KiCad from another CAD application, then KiCad Like a Pro, the video course and eBook, is for you.
Jump to another article
KiCad 6 Guides
0. Why learn KiCad?
1. What is a PCB?
2. The PCB design process
3. PCB fabrication
4. Get KiCad for your operating system
5. An example KiCad project
6. KiCad Project Manager (main window)
7. Overview of the individual KiCad apps
8. KiCad Paths and Libraries
9. Create a new KiCad project from scratch
10. Create a new KiCad project from a template
11. KiCad 6 on Mac OS, Linux, and Windows
12. Major differences between KiCad 6.0 and 5.0
13. KiCad Schematic symbols
14. PCB key terms
Contributed articles
Last Updated 1 year ago.
We publish fresh content each week. Read how-to's on Arduino, ESP32, KiCad, Node-RED, drones and more. Listen to interviews. Learn about new tech with our comprehensive reviews. Get discount offers for our courses and books. Interact with our community. One email per week, no spam; unsubscribe at any time